- Plants
- Profiling line PRO max
PRO max
Your profiling line, if you want to get the best out of the log
The profiling line PRO max is designed for active curve sawing and specialized in value-optimized processing of large quantities of logs. From precise log rotation to active curve resawing or even spline sawing, everything is designed to ensure the optimum cutting pattern for each log, hence achieving the maximum recovery with high-quality lumber. To ensure that our profiling line also achieves the optimum results for you, we adapt the PRO max to your very requirements and down to the smallest detail.
Key data
- Processing up to 400.000 m³ of round logs per year and shift
- Feed speed up to 200 m/min.
- Operating mode: processing of both, sorted and unsorted logs
- Technology: active curve sawing, spline sawing
- Log diameter, large end, up to 60 cm
- Log diameter, small end, from 12 to 53 cm
- Log length 3,00 to 5,20 m
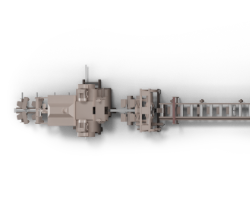
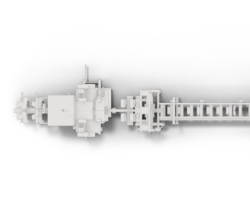
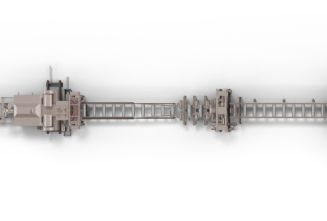
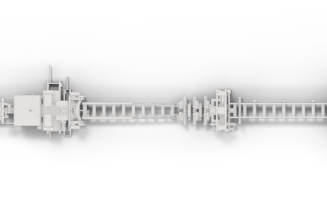
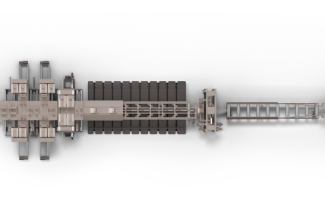
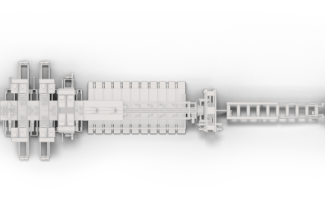
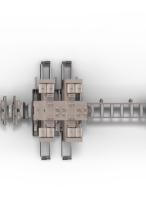
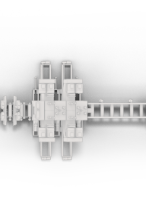
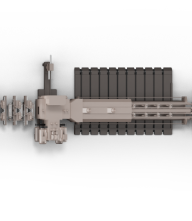
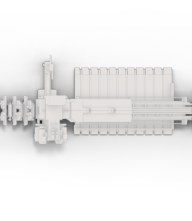
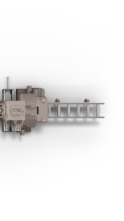
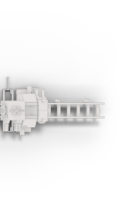
The primary chipper canter group converts the log into a two-sided cant. The logs are fed with either small or large end first, hence making it easy on the log feeding deck and keeping the mechanic simple.
The high-quality chips and sawdust produced are the perfect raw material for pellets and particle board production. This is in line with the LINCK philosophy to process every part of the log with the highest quality standards.
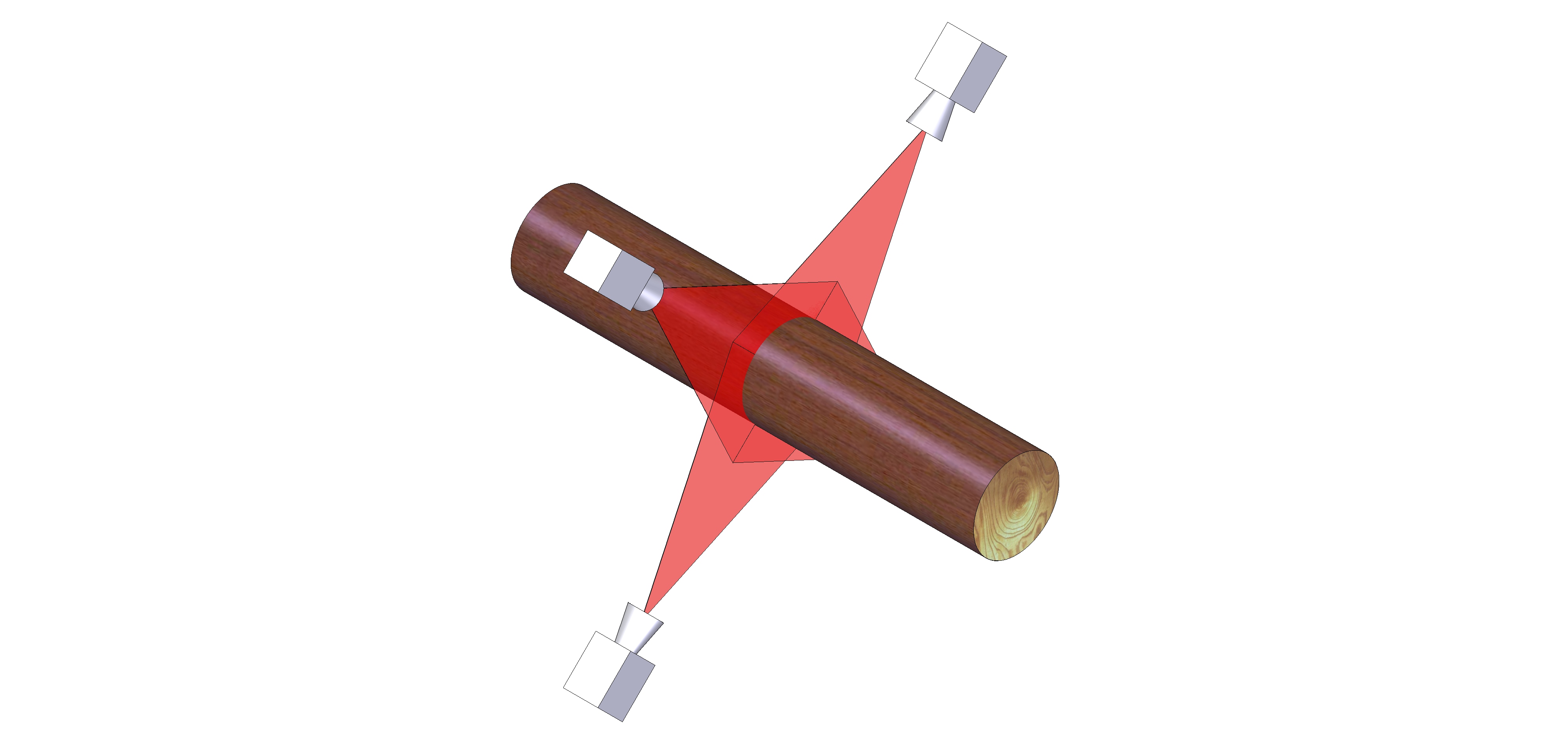
The 3D-scanning is the base for the best possible utilization for each individual log. Based on the collected 3D-data, the LINCK optimizing algorithms will determine the best possible value-optimized sideboard. This interpretation embodies all of LINCK's extensive know-how which will give you the best out of each log.
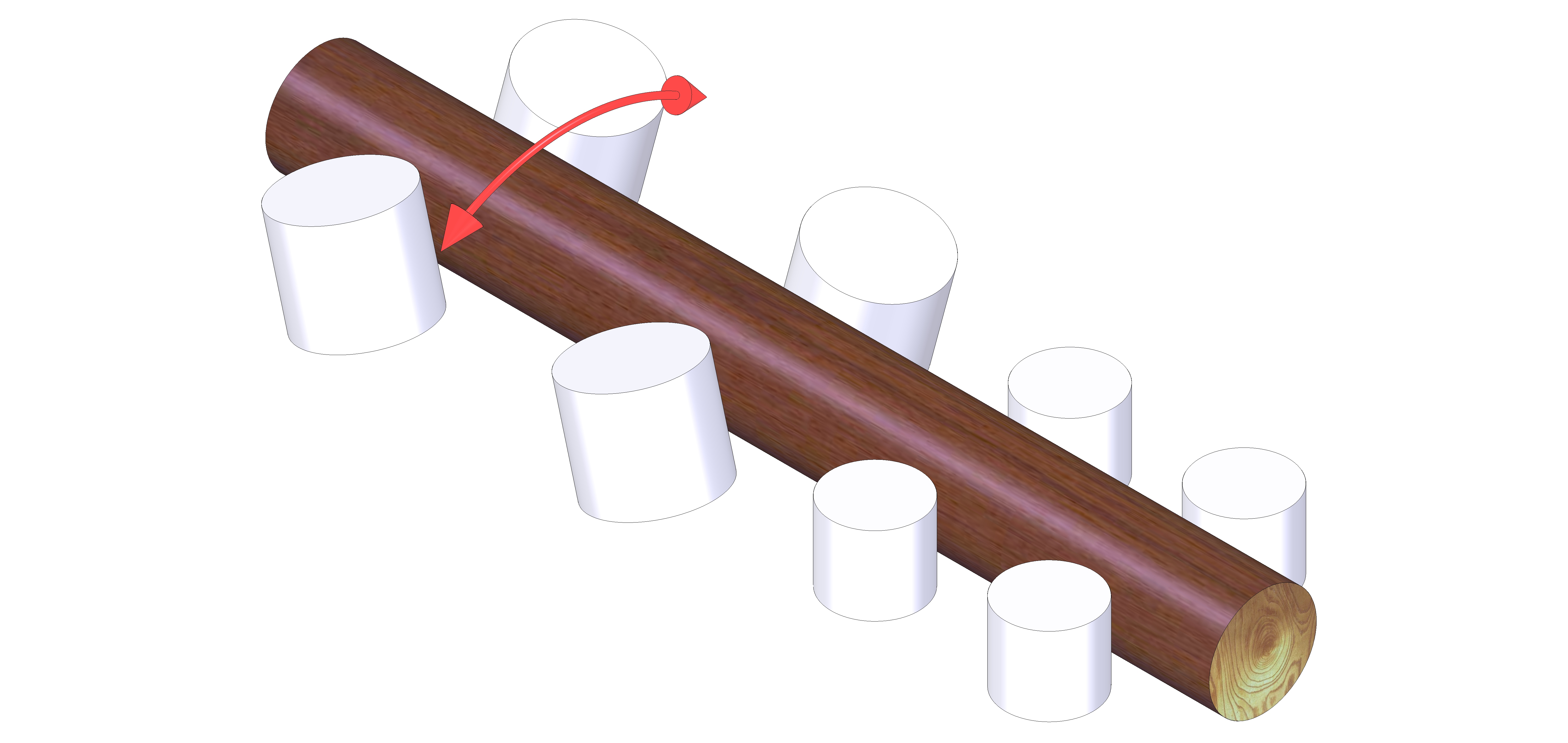
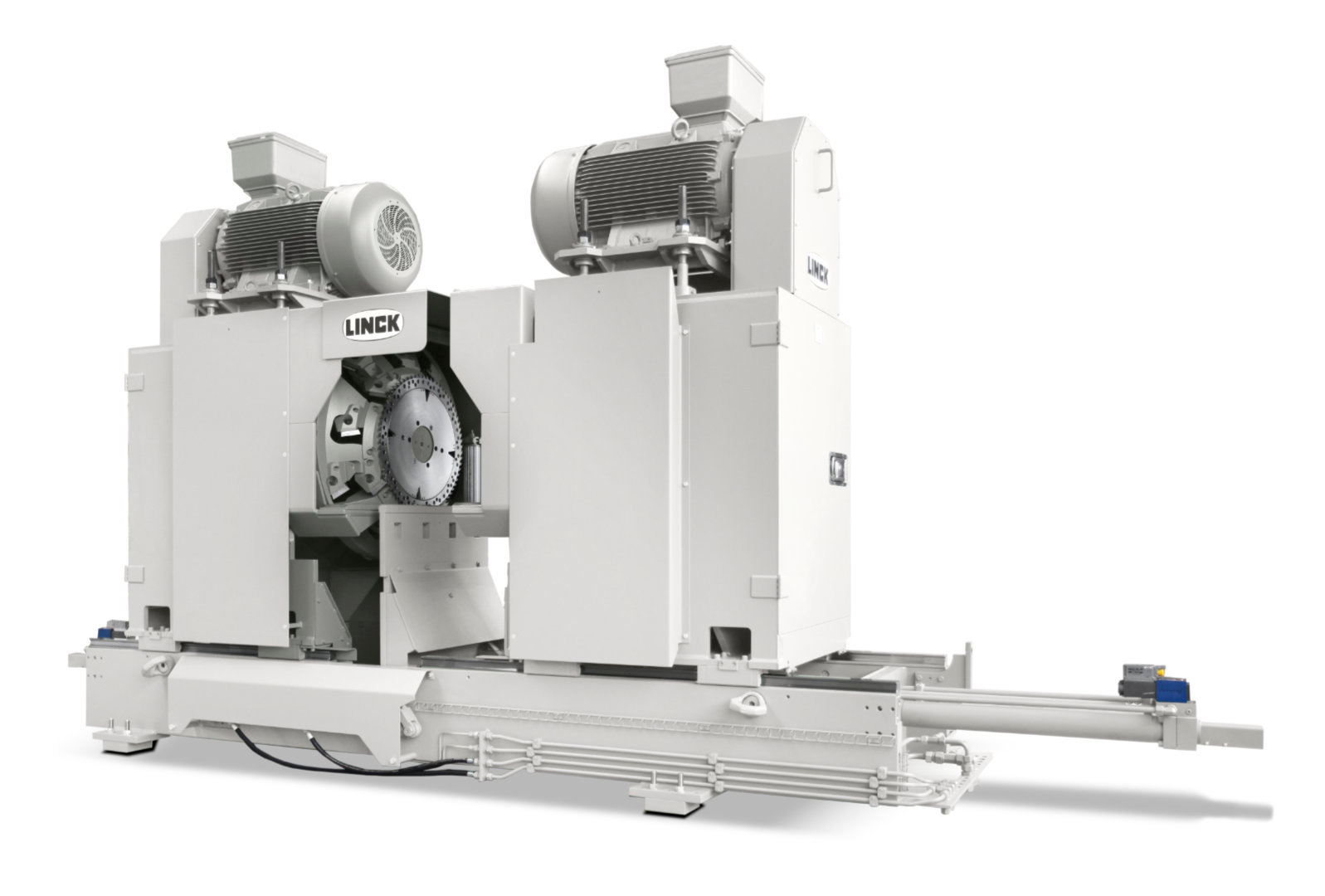
The more precise the infeed, the more accurately the chipper canter can implement the determined cutting pattern. With a standard deviation of +/- 6°, the automatic chipper canter infeed system in a LINCK line is very precise. For comparison: 6° corresponds to one minute on your clock dial.
EV/EVPVM
For converting a two-sided cant into a four-sided one via the secondary chipper canter group, the correct position of the two-sided cant plays an important role: the second chipper canter group actively follows the cant shape, i.e. it does not orient itself to the outer cant contour, but determines an optimum - even spline-shaped - curvature contour. In doing so, it also considers ovality and taper.
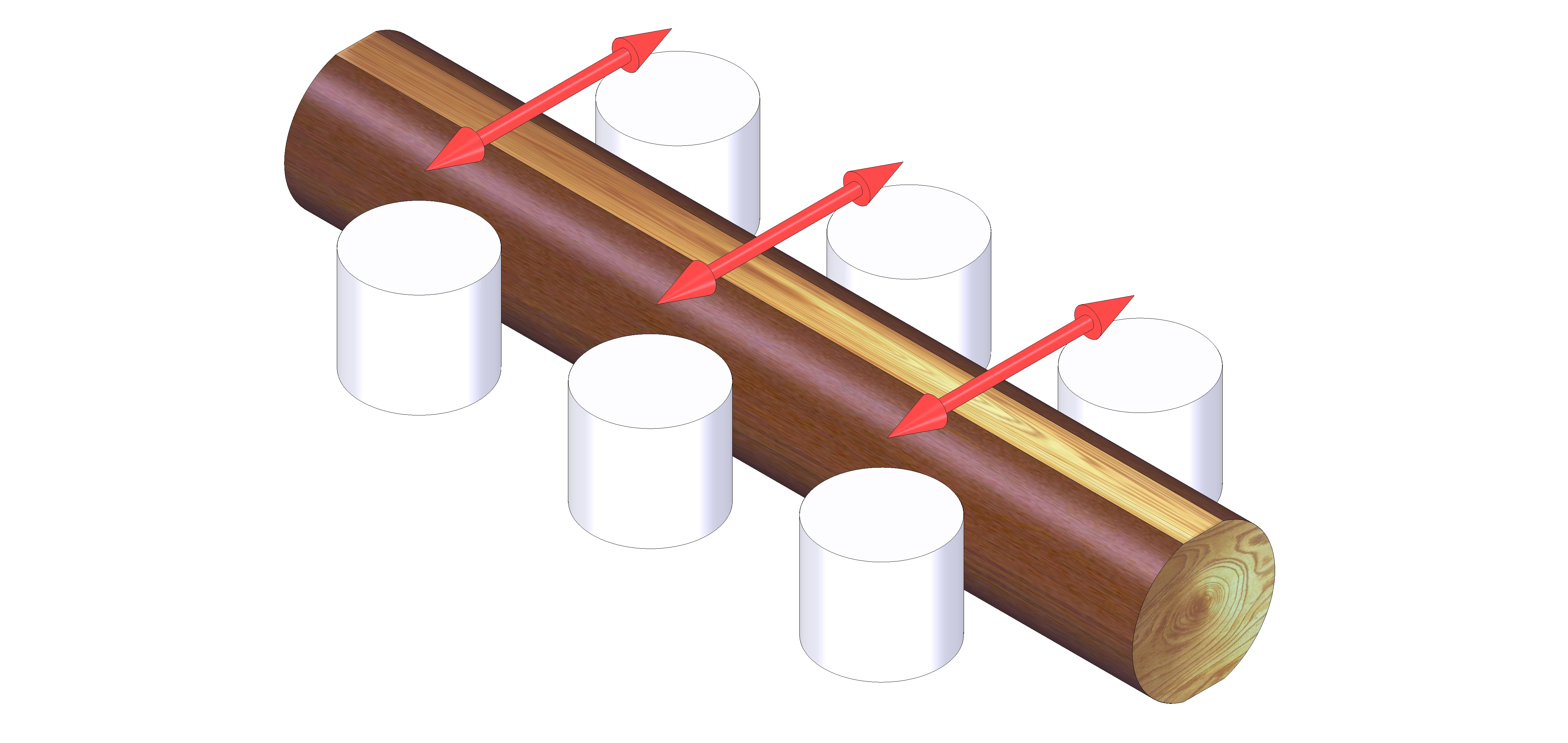
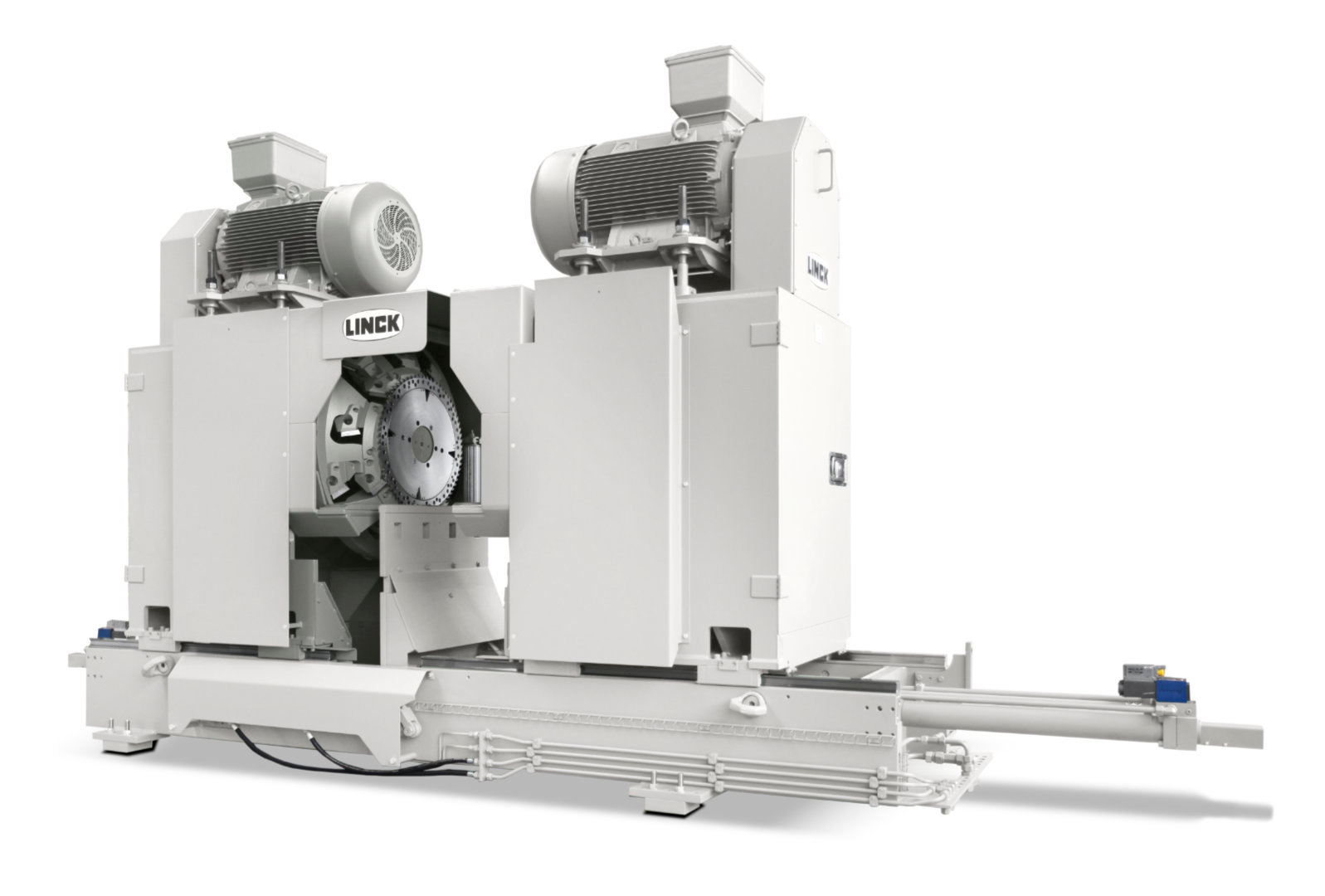
The centering systems in front and behind the machine actively follow the curve or the spline of the cant during its transport. The chipper canter remains in its position, the cant is moved around. Little mass has to be displaced resulting in short adjusting times between the individual cants. Advantage: The gap between the cants is small, the capacity of the saw line increases.
EV/EVPVM
The two profiler units in the primary profiler group produce the sideboards on each side of the cant which are then cut-off by a circular saw. Advantage is the many possibilities to optimize them. Your sideboards are made according to your requirements, e.g. in width, length and position on the side of the cant - even in thickness if so desired. Conical sideboards and sideboards positioned diagonally on the fly along the cant are also possible.
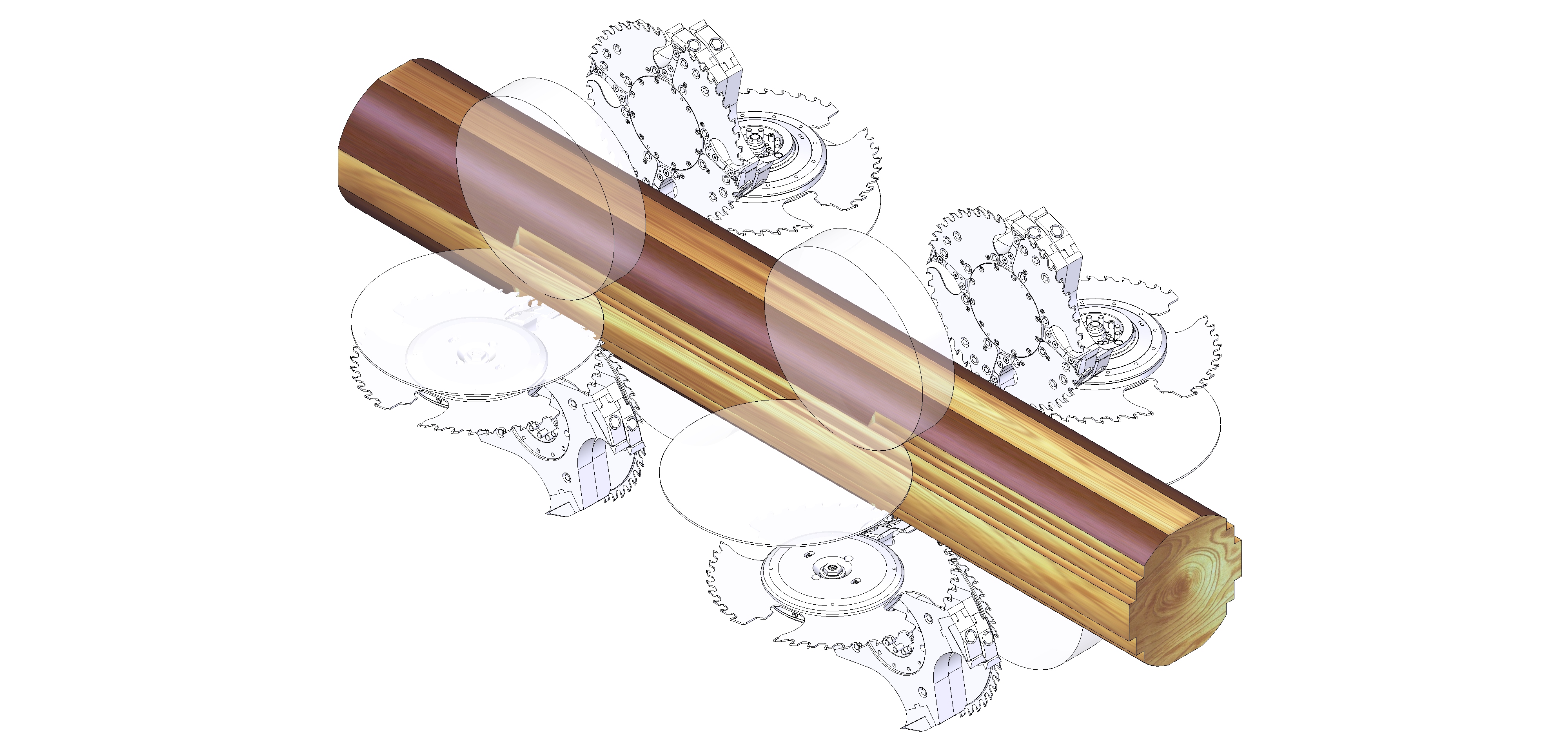
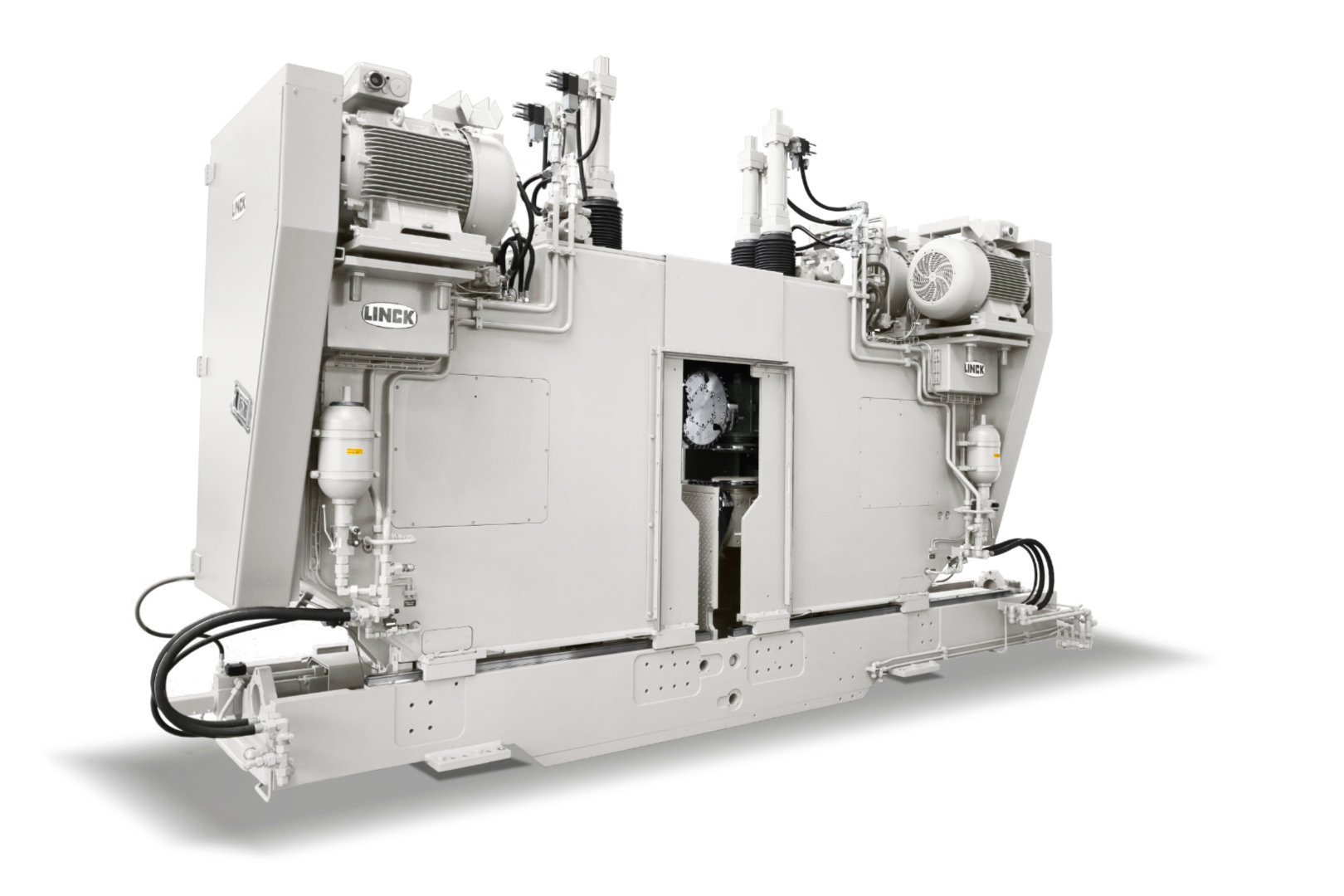
The two profiler units of the primary profiler group optimize the sideboards with highest flexibility: They can - depending on the configuration - vary the sideboards in width, length and even thickness. Optionally they also produce sideboards arranged diagonally and/or conical boards.
VPM
The secondary profiler group produces one or two sideboards on each side of the four-sided cant by actively following the curve or by spline sawing. The centering systems guide the four-sided cant through the machine group following its curve. The machine remains stationary. This means less mass has to be moved and adjusting times and gaps between the cants are reduced.
A large number of horizontal and vertical servo-hydraulic rollers in the centering systems create the curvature and hold the four-sided cant in a stable position. The vertical rollers provide the curve, the horizontal rollers together with the vertical ones ensure the stable cant position. As the profiler units remain in their position, less mass has to be moved which reduces the gap between the cants and increases the saw line productivity.
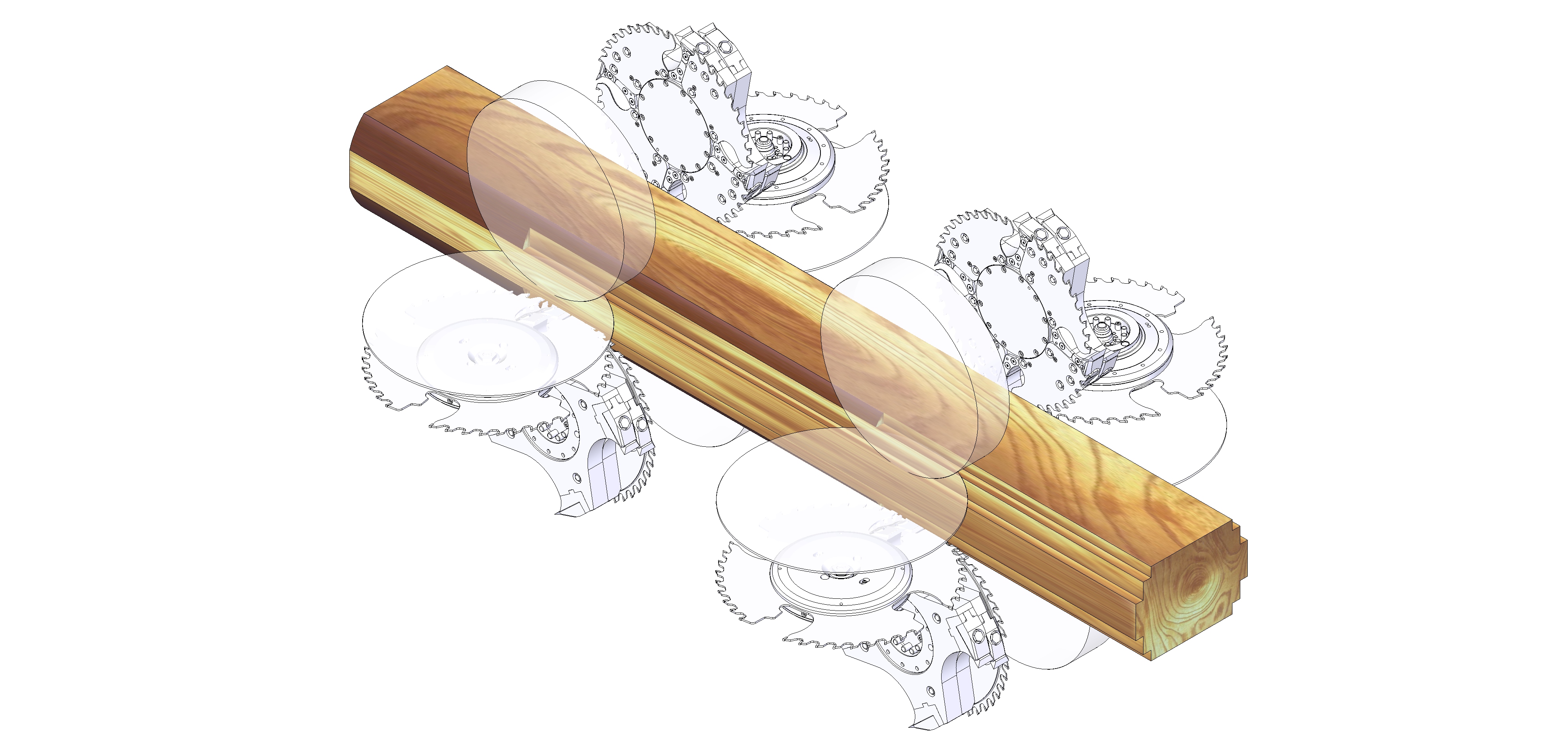
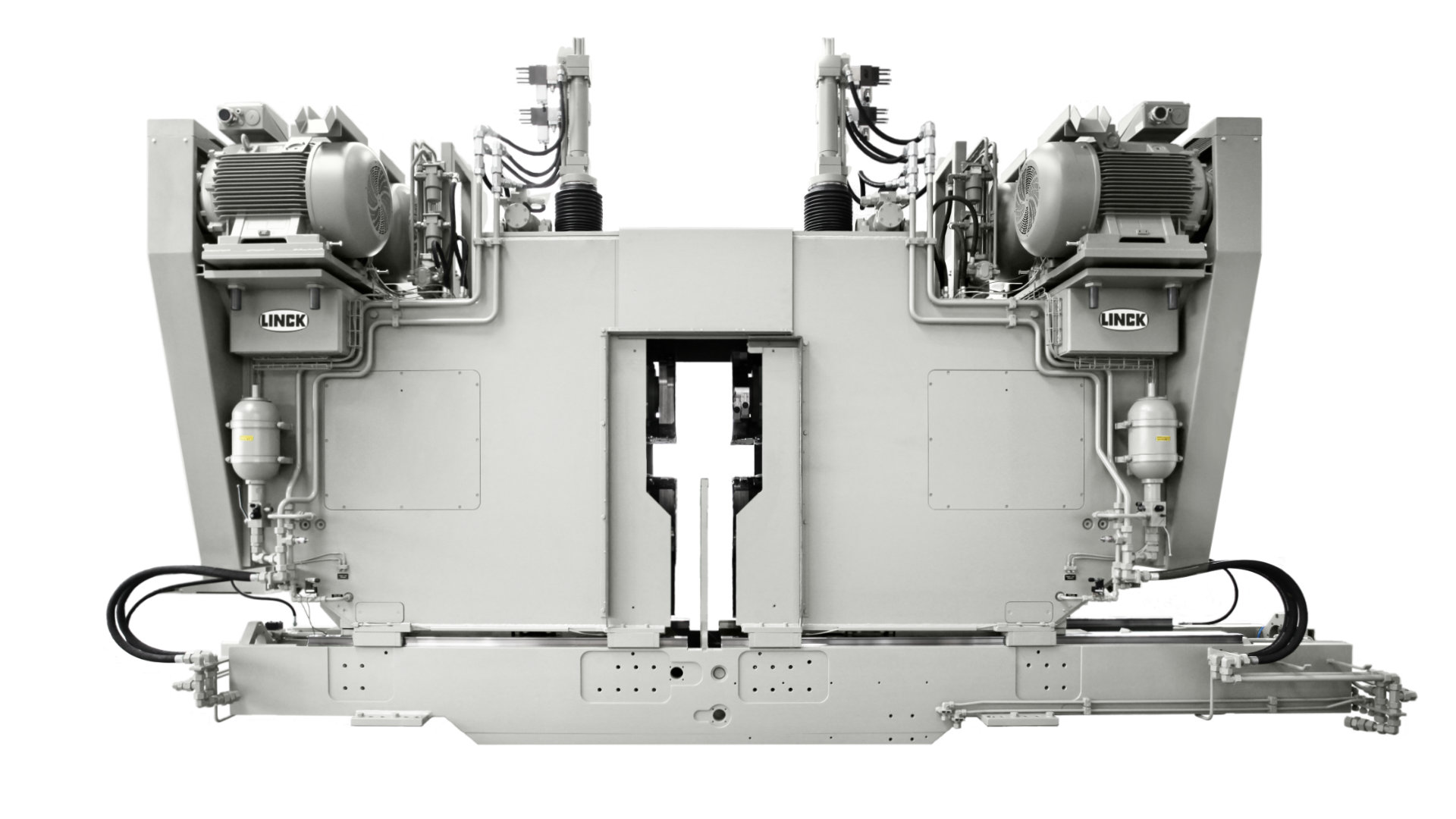
The two profiler units of the secondary profiler group optimize the sideboards with highest flexibility: They can - depending on the configuration - vary the sideboards in width, length and even thickness.
VPM
The split saw cuts off the sideboards from the centre products in one work step which allows for larger - also spline-shaped - curvatures. The separating conveyor then takes the sideboards to the sorting plant. Its great advantage: It can also handle multiple centre products and sideboards.
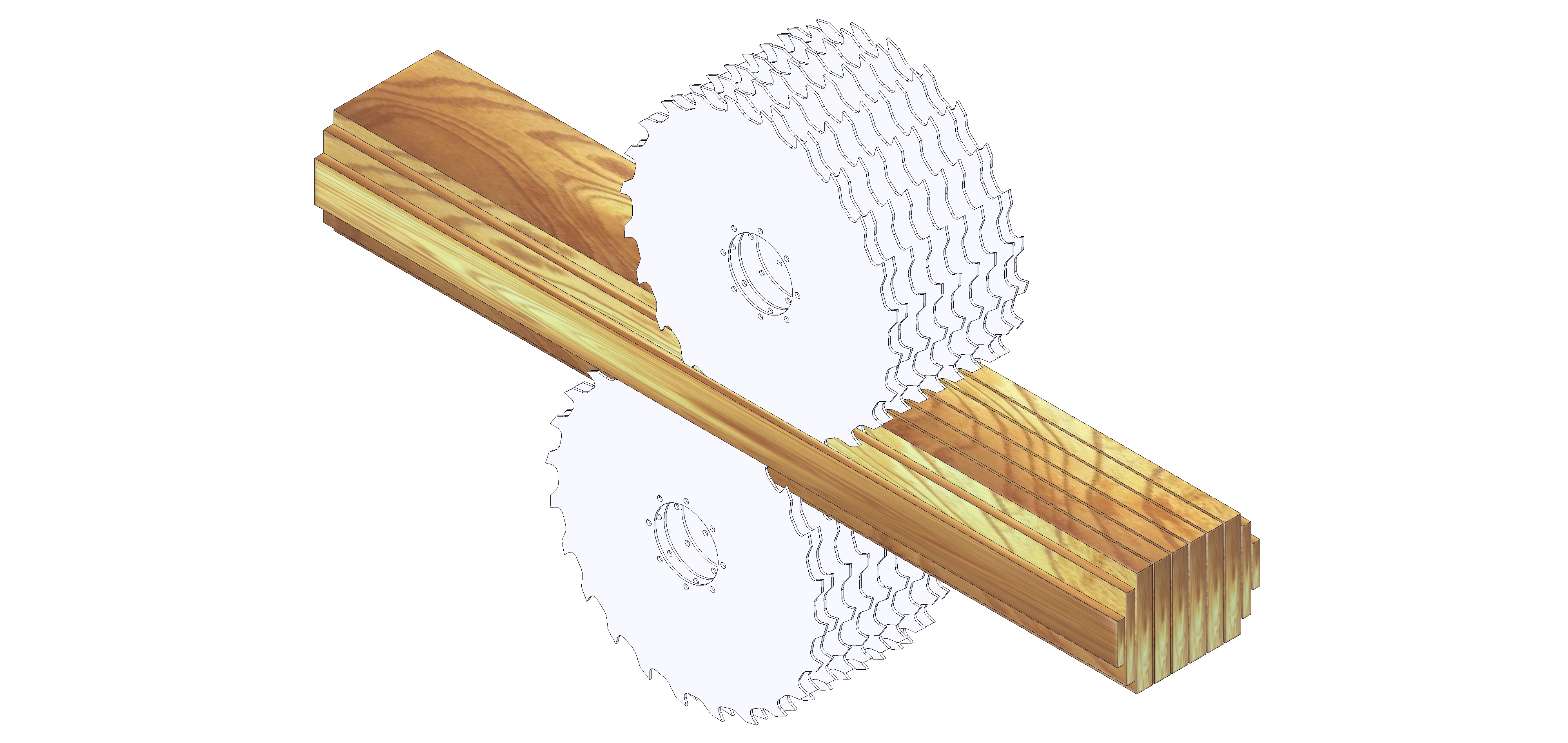
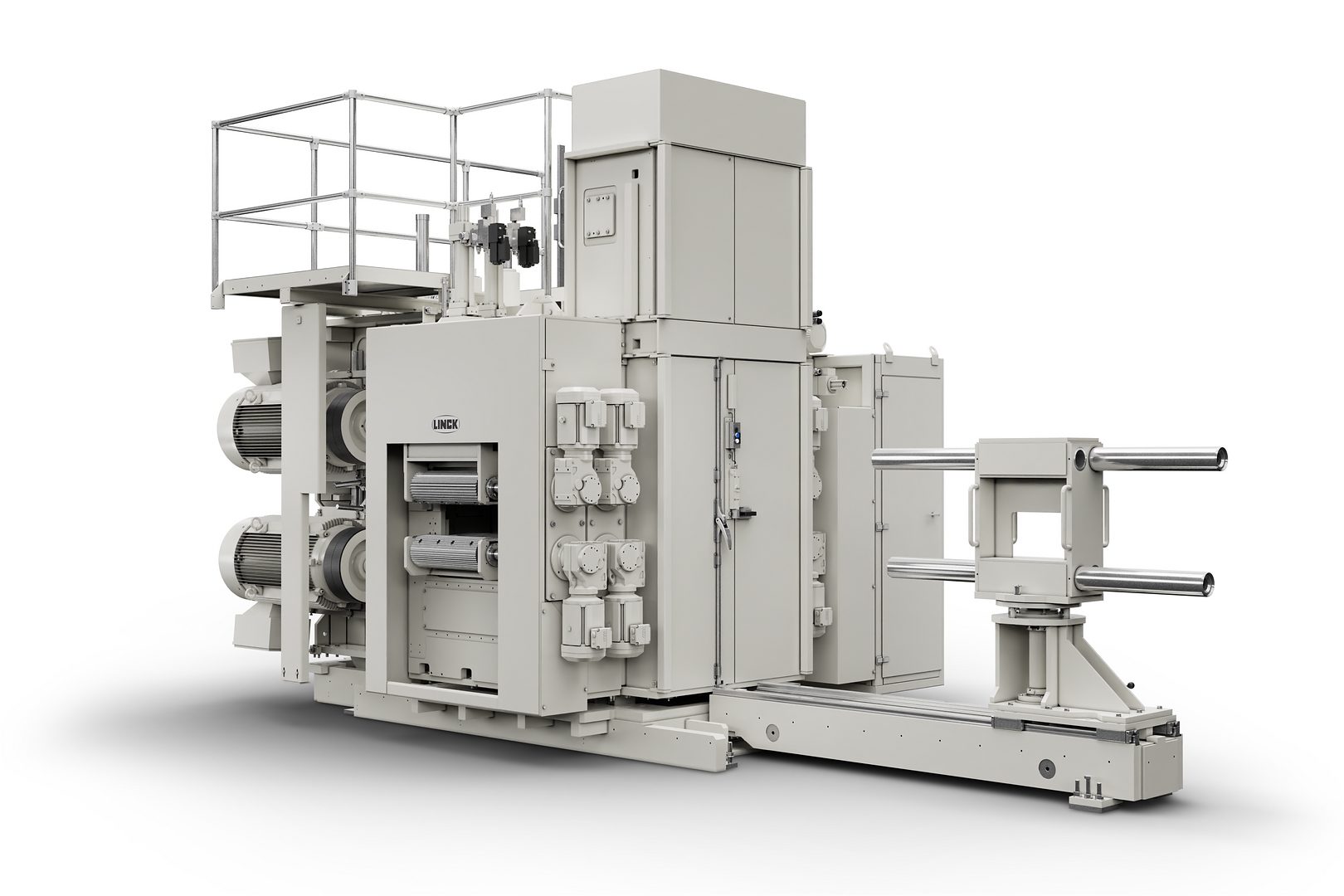
The split saw works according to the double arbor principle with two saws reducing saw kerf as the cutting forces can be distributed to two sawblades.
MKS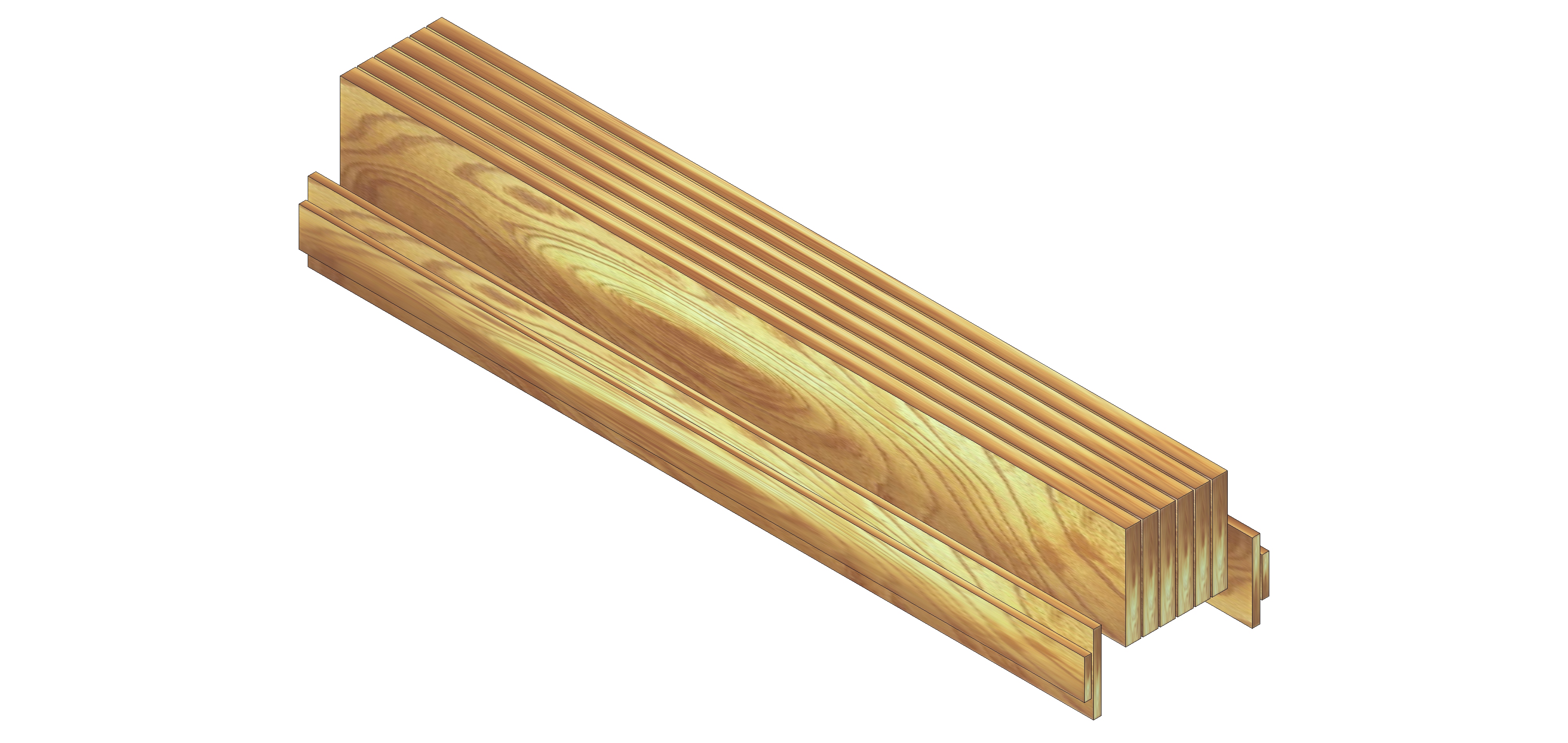
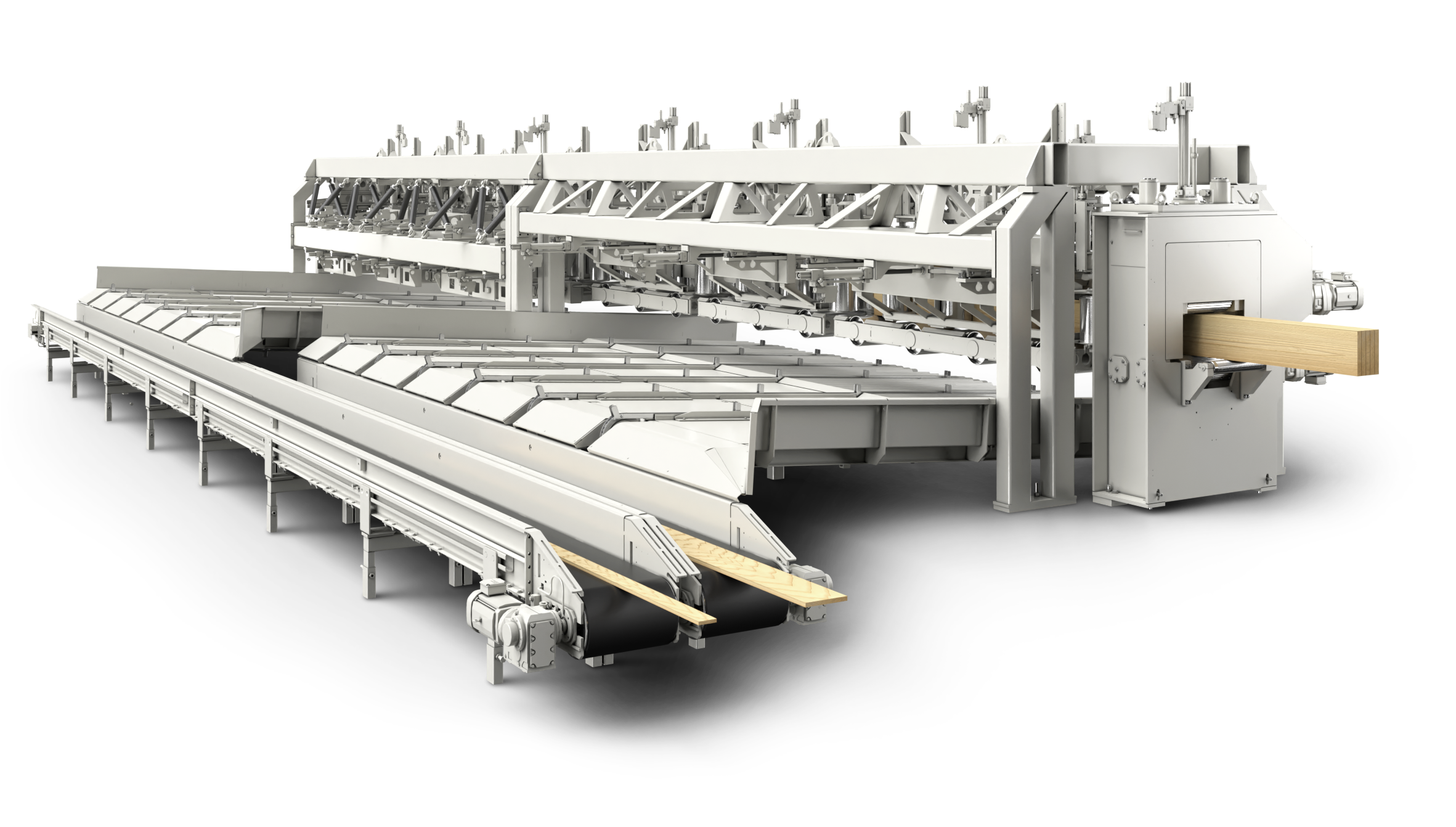
The separating conveyor reliably separates the sideboards from the centre products, even with multiple centre products.
The horizontal circular split saw produces quarter timber exactly to your requirements. It splits the centre products horizontally and turns five, for example, into ten or fifteen boards. The sawblades run on two independently operating tool axes.
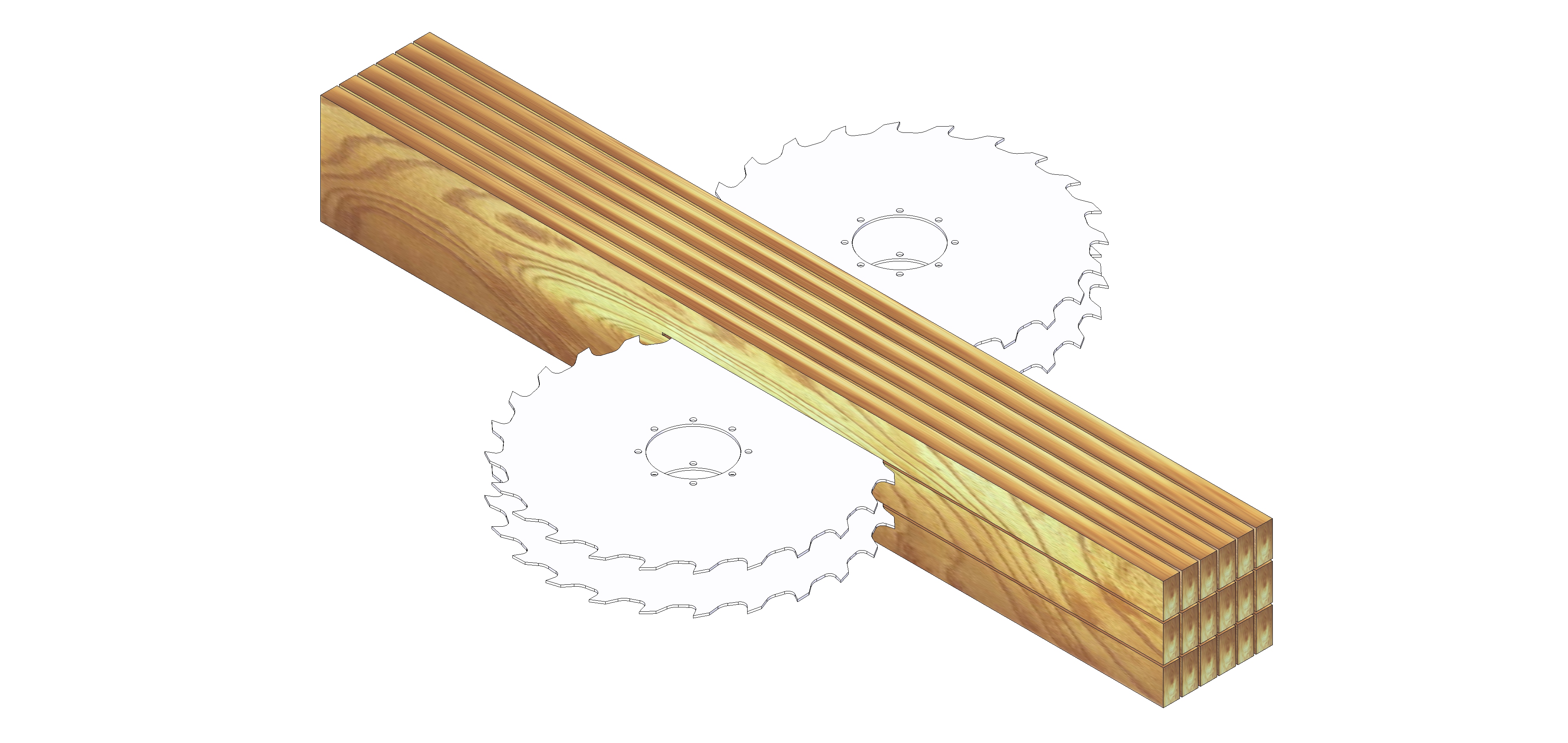
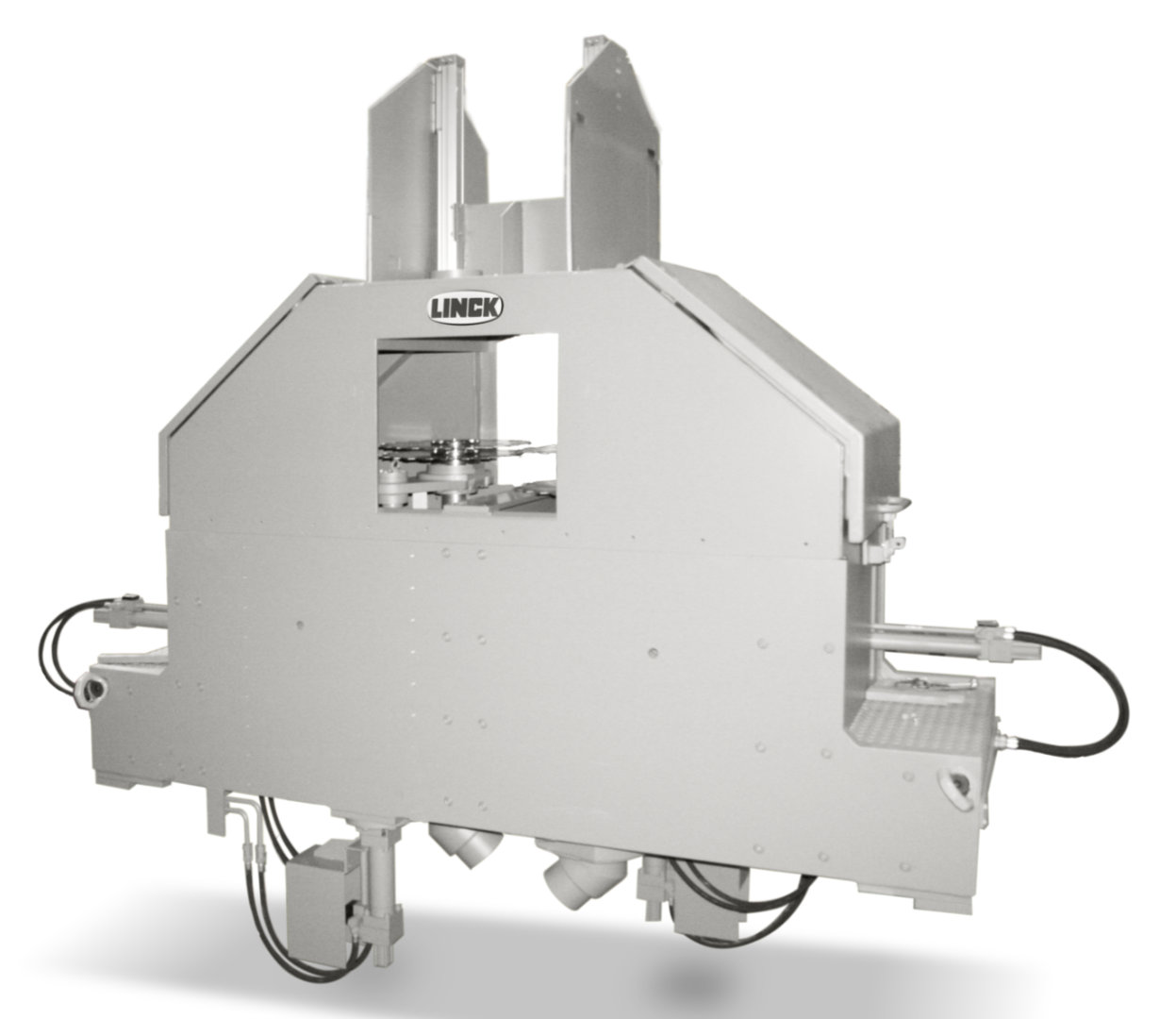
The horizontal circular split saw works according to the double arbor principle with two saws reducing saw kerf as the cutting forces can be distributed to two sawblades.
HKM