PRO SL
Your solution for the economical production of pallet components
The profiling line PRO SL is LINCK's special solution for profiling short logs. It produces pallet boards and components from short logs. The saw line processes pre-sorted logs in accordance with predetermined, fixed cutting patterns. This means, the log gap can be very small which contributes to the high production capacity of the saw line. Together with you, we make the short log profiling line PRO SL your solution for the economical production of pallet boards.
Key data
- Processing up to 150.000 m³ of round logs per year and shift
- Feed speed from 30 to 110 m/min. and more depending on the configuration
- Operating mode: processing of sorted logs
- Log diameter, large end, up to 45 cm
- Log diameter, small end, 10 cm
- Log length 1,20 to 2,80 m
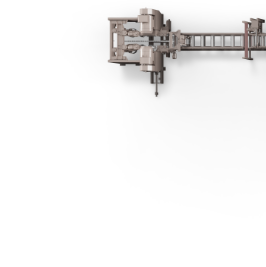
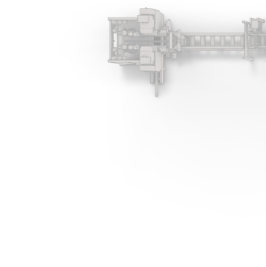
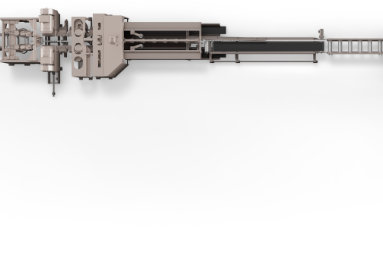
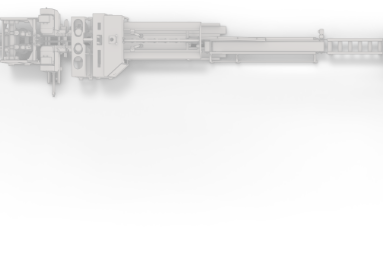
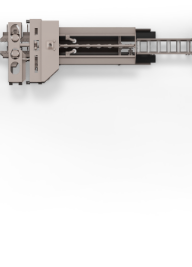
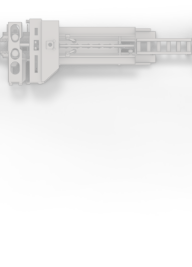
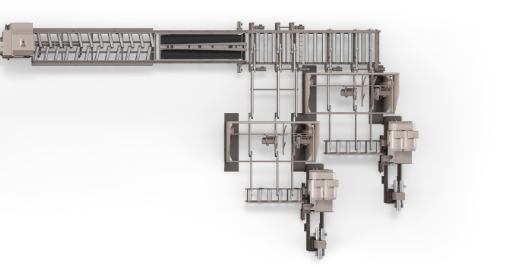
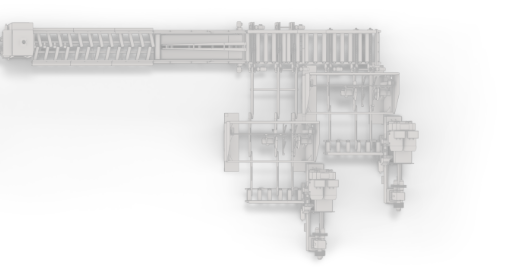